當(dāng)用高粘度材料成型厚壁產(chǎn)品時(shí),注塑模具產(chǎn)品表面的橘皮或表面起皺缺陷一般發(fā)生在流道末端。例如注塑模具產(chǎn)品在注塑過程中,如果熔體流動(dòng)速率過低,注塑模具就會(huì)失效。加工品表面會(huì)迅速凝固,隨著流動(dòng)阻力的增大,熔體前端流動(dòng)變得不均勻,導(dǎo)致先凝固的外層材料不能充分接觸型腔壁,導(dǎo)致皺紋。這些褶皺在固化和包裝后成為無法修復(fù)的缺陷。
When thick wall products are molded with high viscosity materials, orange peel or surface wrinkling defects usually occur at the end of the runner. For example, in the injection process of injection mold products, if the melt flow rate is too low, the injection mold will fail. The surface of the processed product will solidify rapidly. With the increase of flow resistance, the flow at the front end of the melt becomes uneven, resulting in that the solidified outer material can not fully contact the cavity wall, resulting in wrinkles. These folds become irreparable defects after curing and packaging.
注塑模具加工產(chǎn)品表面的橘皮缺陷影響表面外觀。所以在此建議您采用提高熔體溫度、提高注射速度、適當(dāng)提高注塑模具加工溫度等方法來解決這一缺陷。
Orange peel defects on the surface of injection mold products affect the surface appearance. Therefore, it is recommended that you solve this problem by increasing the melt temperature, increasing the injection speed and appropriately increasing the processing temperature of the injection mold.
此外模具設(shè)計(jì)缺陷也會(huì)在澆口附近產(chǎn)生暗斑。澆口處尖銳的轉(zhuǎn)角能夠通過改變半徑來避免,在設(shè)計(jì)時(shí)要留心澆口的位置和直徑,看看澆口的設(shè)計(jì)是否合適。
In addition, mold design defects will also produce dark spots near the gate. Sharp corners at the gate can be avoided by changing the radius. Pay attention to the position and diameter of the gate in the design to see if the gate design is appropriate.
暗斑不但會(huì)發(fā)生在澆口位置,而且也經(jīng)常會(huì)在制品尖銳的轉(zhuǎn)角形成后出現(xiàn)。例如,制品的尖銳轉(zhuǎn)角表面一般非常光滑,但是在其后面就非?;野登掖植?。這也是由于過高的流速和注射速度致使冷卻表面層被內(nèi)部流體取代發(fā)生滑動(dòng)而造成的。
Dark spots not only occur at the gate, but also often occur after sharp corners of the product are formed. For example, the sharp corner surface of the product is generally very smooth, but behind it is very gray and rough. This is also caused by the sliding of the cooling surface layer replaced by the internal fluid due to the high flow rate and injection speed.
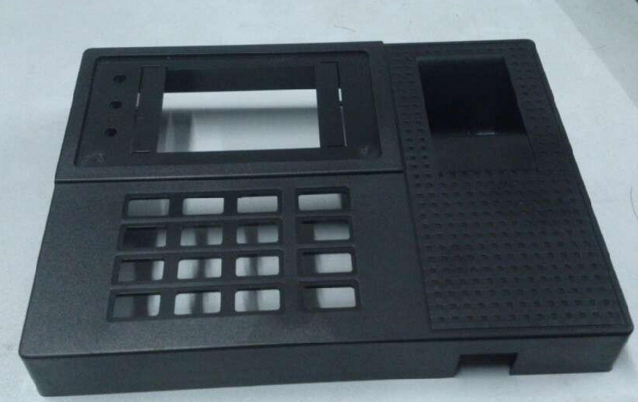
再次推薦采用分步注射并逐漸增加注射速度。佳的方法是允許熔體只是在流過銳角邊緣后其速度才開始增加。
It is again recommended to use step-by-step injection and gradually increase the injection speed. A good method is to allow the melt to increase its velocity only after flowing through the sharp edge.
對(duì)于注塑加工制品來說,在有紋理的制品表面,其光澤的不同是為明顯的。即使模具的表面十分均勻,不規(guī)則的光澤也可能出現(xiàn)在制品上。也就是說,制品某些部位的模具表面效果沒有很好地得以重現(xiàn)。
For injection molded products, the difference in gloss is obvious on the surface of textured products. Even if the surface of the mold is very uniform, irregular gloss may appear on the product. In other words, the mold surface effect of some parts of the product is not well reproduced.
另外,
濟(jì)南注塑模具廠家提醒,熔體不充分的排氣也是造成此缺陷的一個(gè)原因。“橘皮”或者表面起皺缺陷一般發(fā)生在用高粘度材料成型厚壁制品時(shí)的流道末端。在注射過程中,若熔體流動(dòng)速度過低,制品表面會(huì)迅速固化。
In addition, Jinan injection mold manufacturers remind that insufficient exhaust of melt is also a reason for this defect. "Orange peel" or surface wrinkling defects usually occur at the end of the runner when forming thick wall products with high viscosity materials. During the injection process, if the melt flow rate is too low, the product surface will solidify rapidly.
隨著流動(dòng)阻力的加大,熔體前端流將會(huì)變得不均勻,致使先固化的外層材料不能與型腔壁充分接觸,從而產(chǎn)生了皺褶。這些皺褶經(jīng)過固化和保壓后就會(huì)變成不可消除的缺陷。對(duì)于該缺陷,解決的方法是提高熔體溫度并且提高注射速度。
With the increase of flow resistance, the melt front-end flow will become uneven, so that the solidified outer material can not fully contact with the cavity wall, resulting in wrinkles. These wrinkles will become irreparable defects after curing and pressure maintaining. For this defect, the solution is to increase the melt temperature and the injection speed.
模具注塑加工制品表面橘皮及暗斑存在原因以及怎么處理的相關(guān)內(nèi)容都給介紹了,您可以作為參考使用,當(dāng)然了解更多信息可以關(guān)注我們網(wǎng)站
tongbang.net.cn!
The causes of orange peel and dark spots on the surface of injection molded products and how to deal with them are introduced. You can use them as a reference. Of course, for more information, you can pay attention to our website www.sdlqmj com!